INSTRUCTION AND CALCULATION ABOUT STRENGTH
MARINE HYDRAULIC CYLINDER-FYG72-220-120G-1480-00
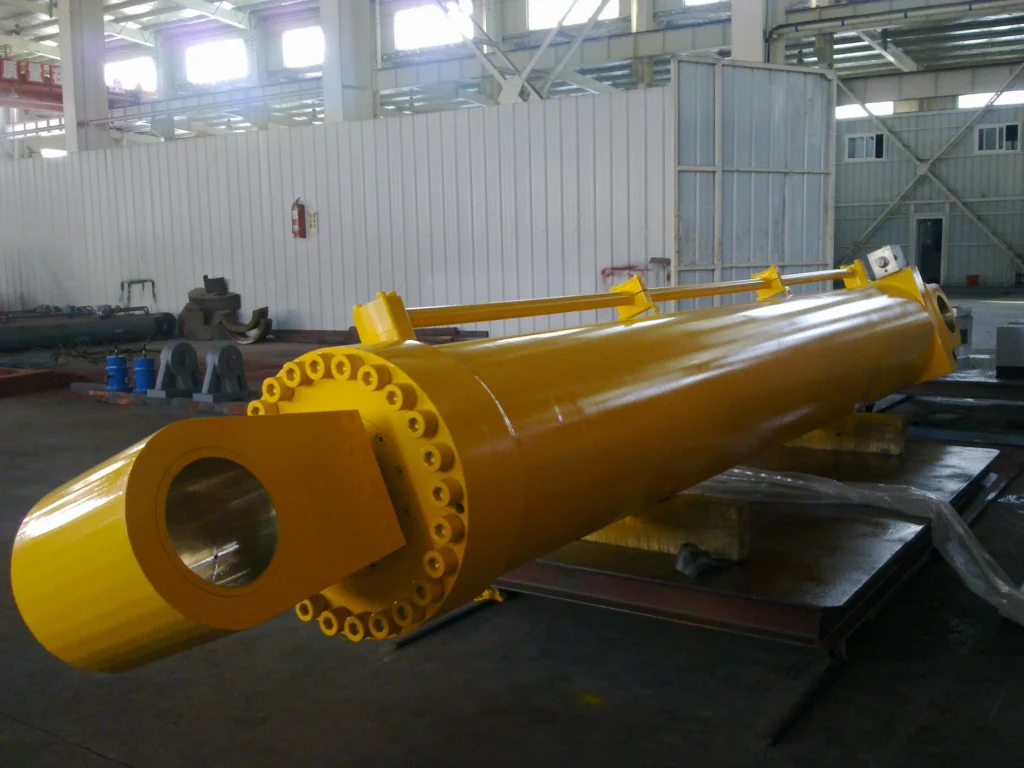
Description
In the demanding marine environment, hydraulic cylinders are subjected to extreme conditions such as corrosive saltwater, high-pressure loads, dynamic wave forces, and temperature fluctuations. Ensuring the structural integrity of these critical components through rigorous strength calculations is paramount. Proper design validation prevents catastrophic failures that could endanger crew safety, disrupt operations, or cause environmental harm from oil leaks. Strength calculations verify that cylinders withstand operational stresses, including hoop stress in the barrel, buckling resistance in the piston rod, and fatigue from cyclic loads. Compliance with international standards (e.g., ISO, DNVGL) and corrosion-resistant material selection further enhance reliability and longevity. By prioritizing precise strength analysis, marine engineers mitigate risks, extend equipment lifespan, and uphold compliance with stringent maritime regulations—safeguarding both human lives and ocean ecosystems.
To calculate the hydraulic cylinder pressure required to generate a specific force, follow these steps:
Parameters: double action hydraulic cylinder, cylinder tube OD=270MM, ID=220MM, piston rod OD=120MM, test pressure: 250bar
- calculation about welding strength for tube and end cap
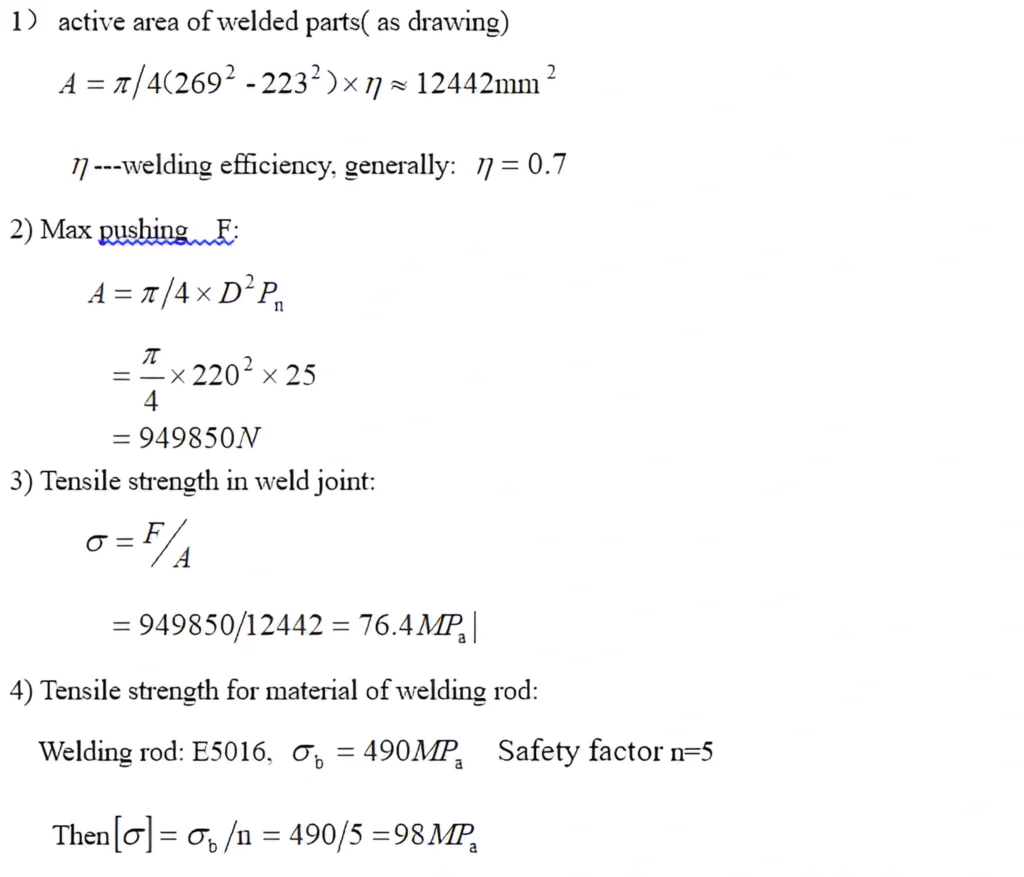
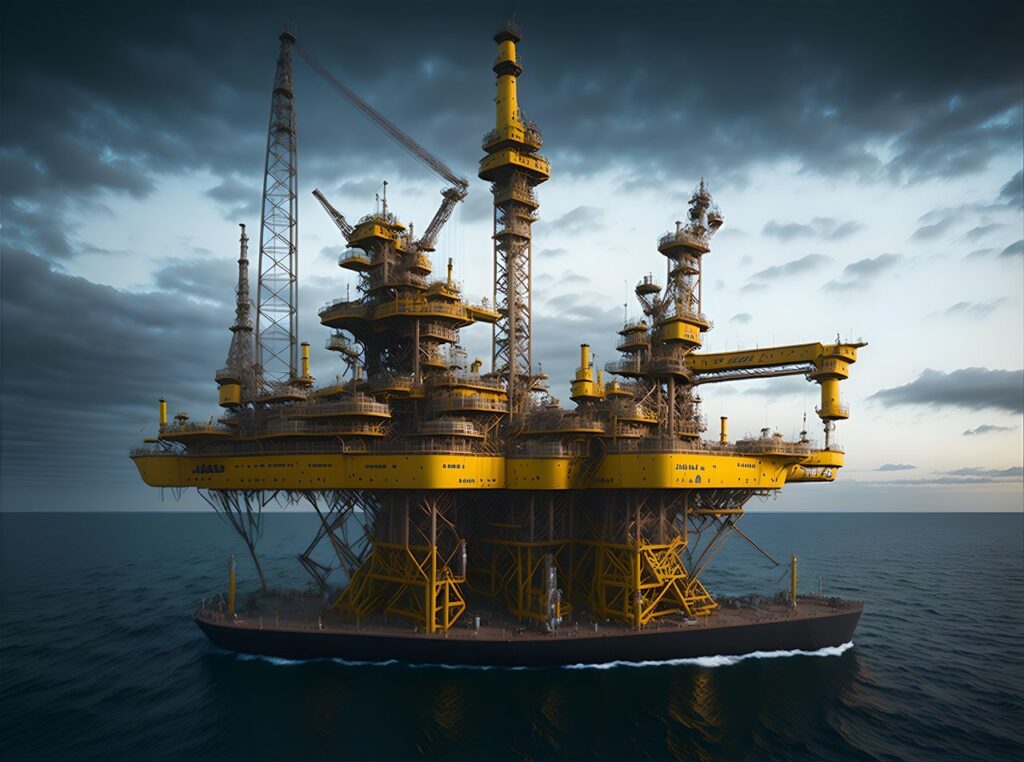
- calculation for wall thickness of cylinder tube:
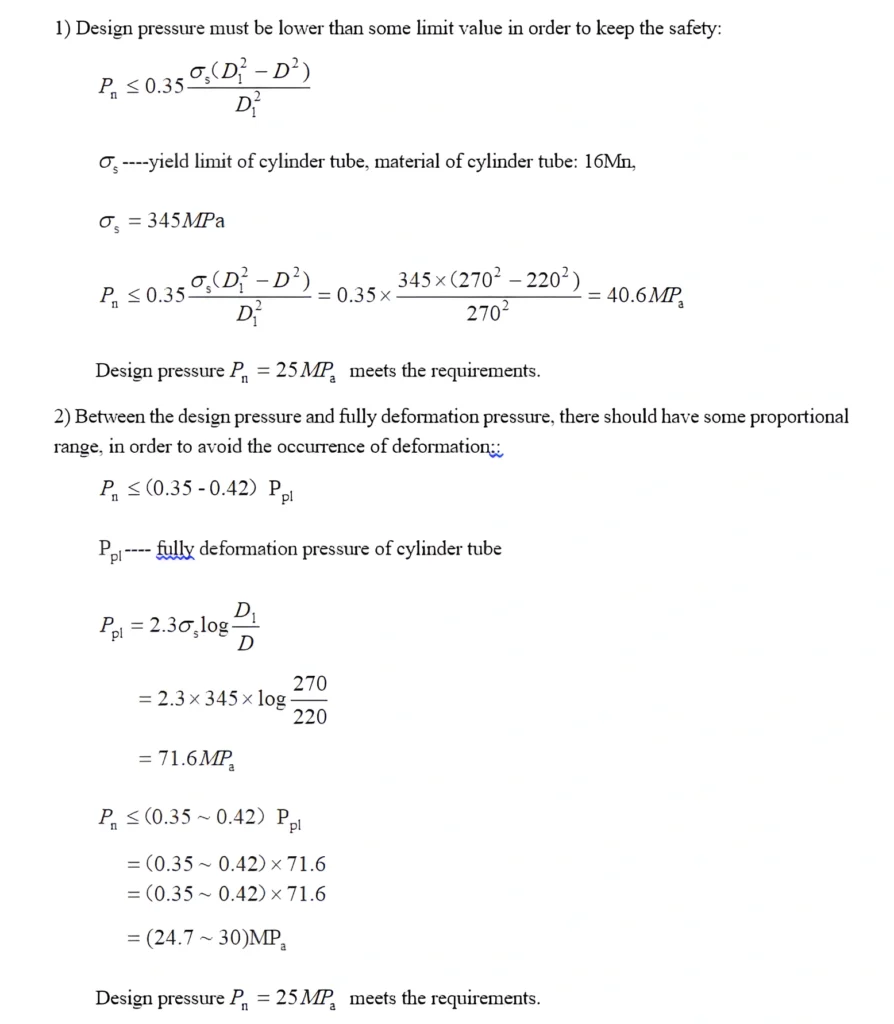
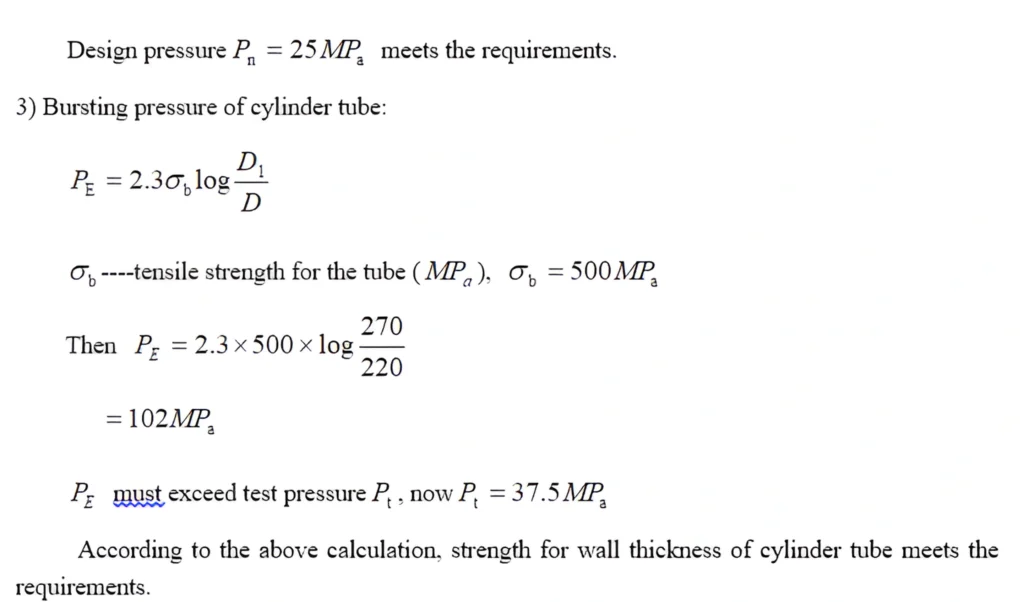
- strength of screw joint in piston and piston rod
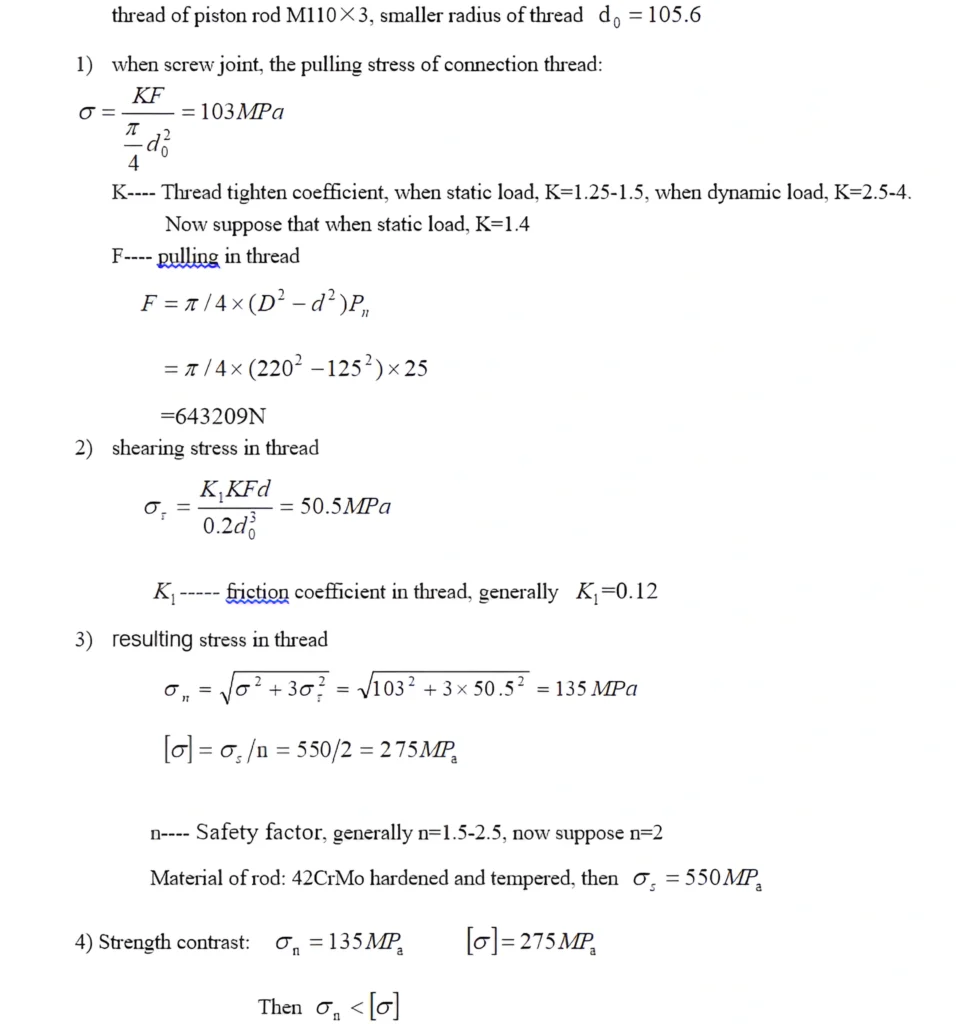
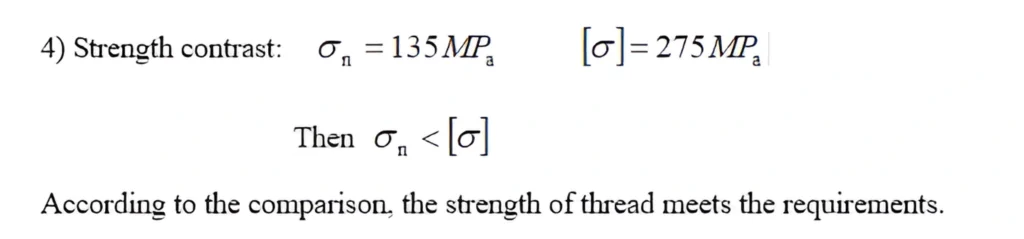
- The strength of screw joint in connector and piston rod
Thread in connector and piston rod M110×3 is the same as thread in piston and piston rod, so the strength of thread in piston rod meets the requirements.
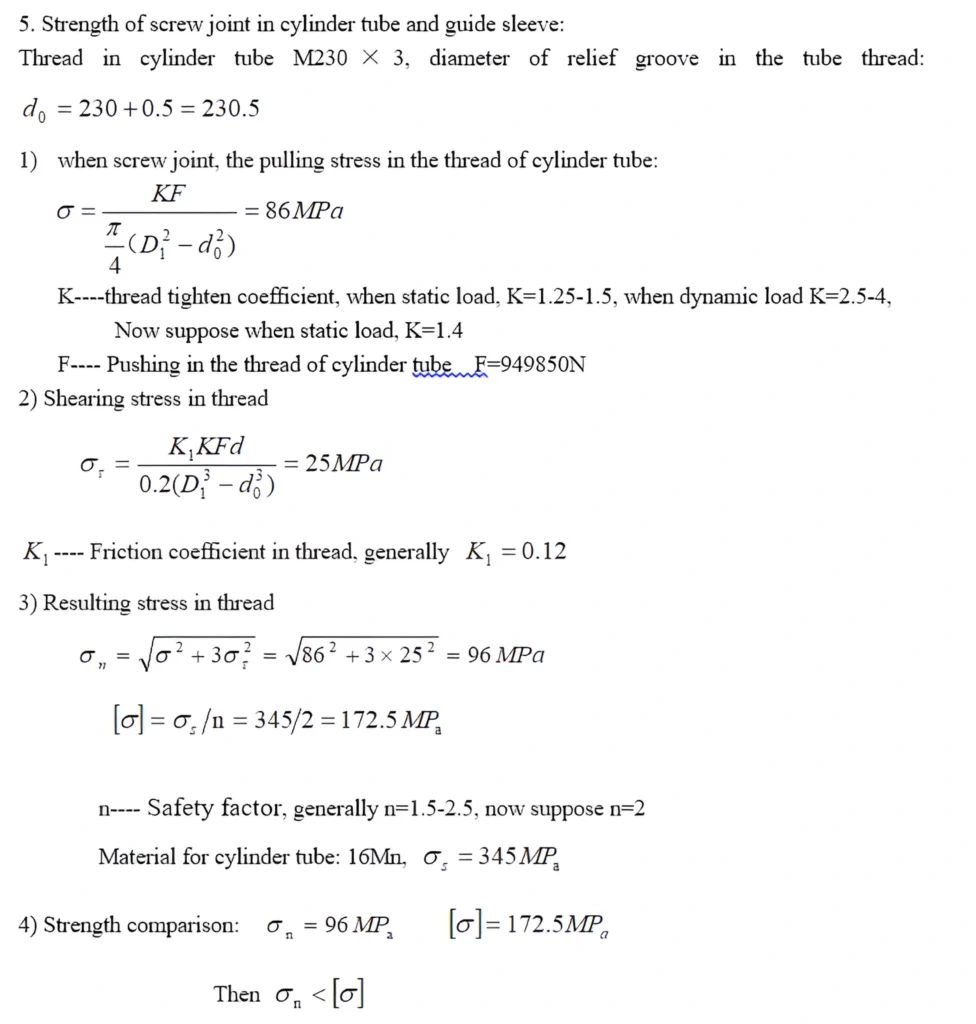
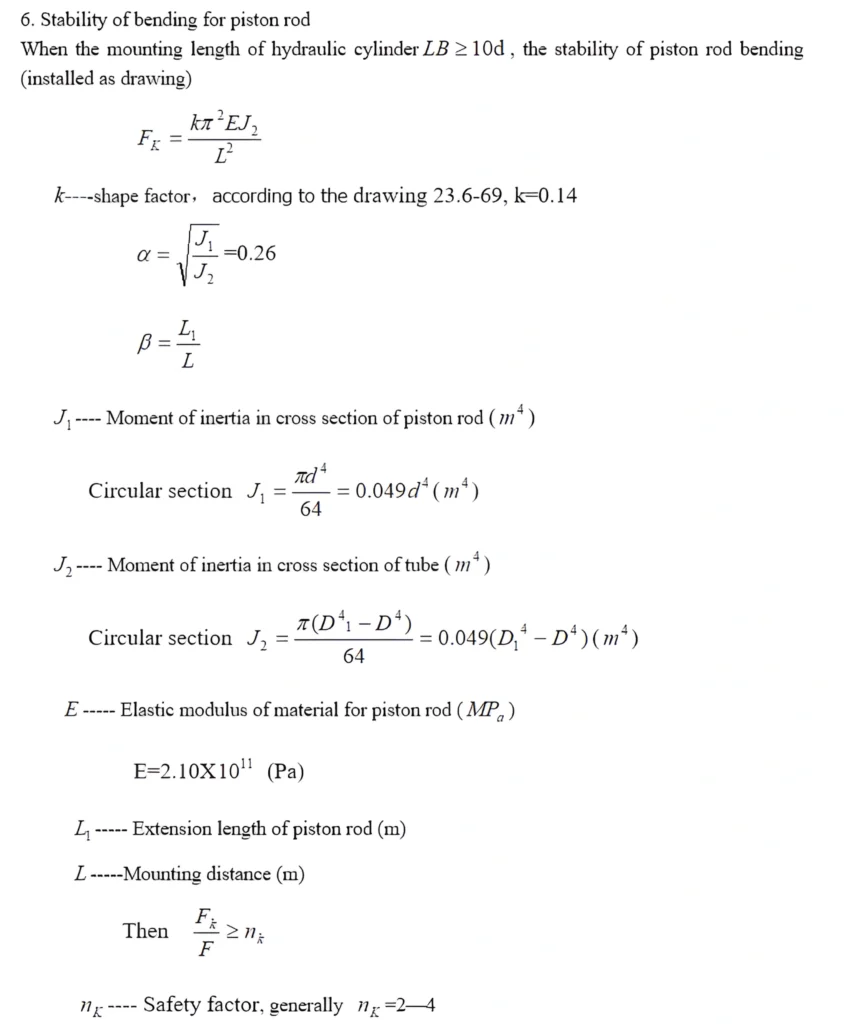
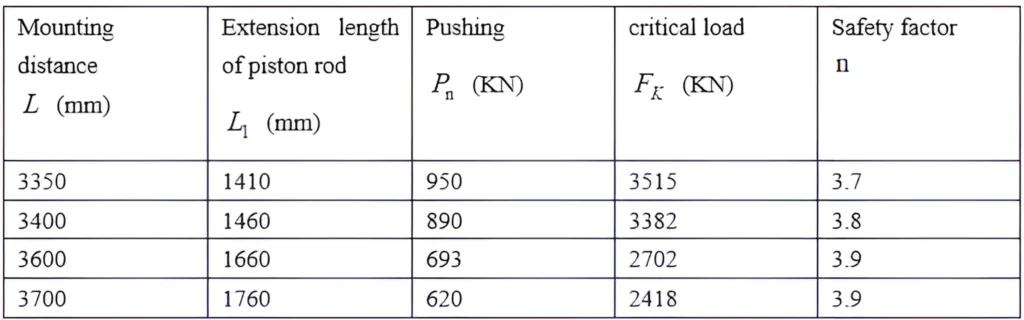
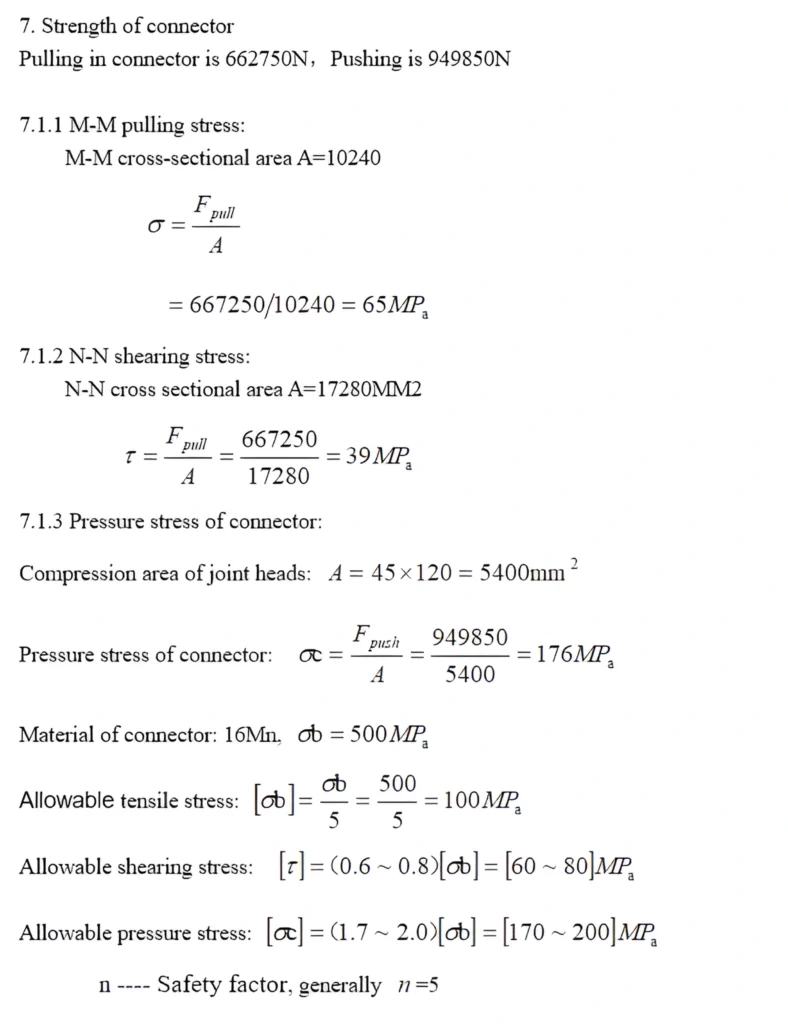
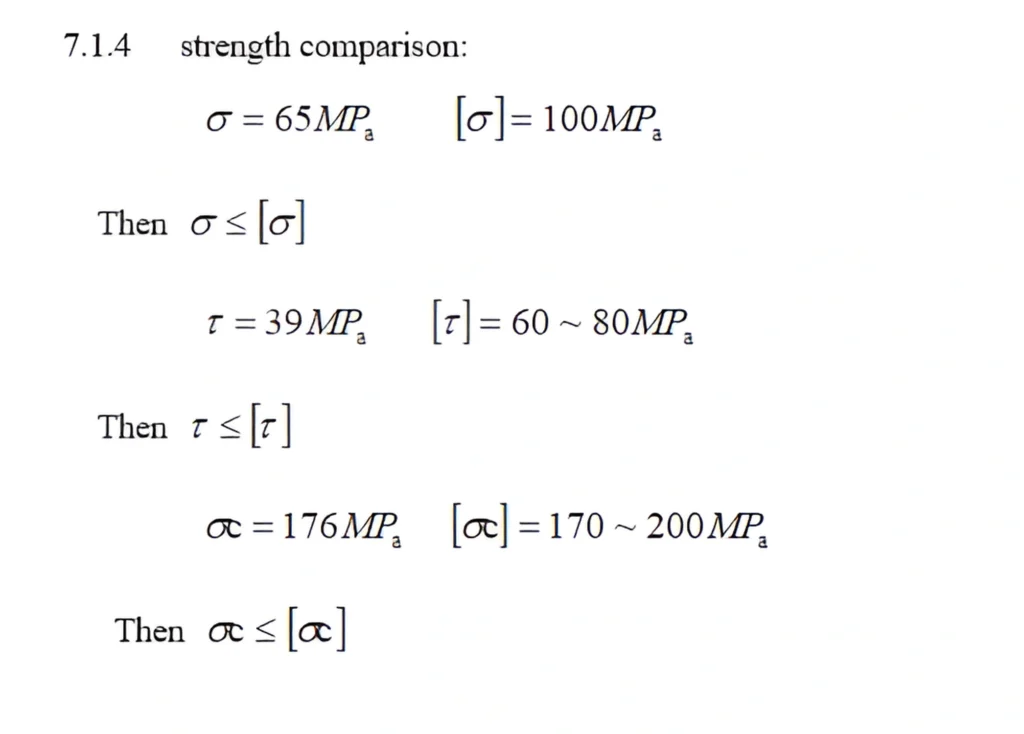
According to the comparison, the strength of connector meets the requirements.
As the size of back ear is the same as the size of connector and material, so the strength of back ear meets the requirements.