Comparative Study of Domestic and International Hydraulic Coating Technologies
Introduction
Hydraulic cylinders are critical actuators in hydraulic systems, widely applied in engineering machinery. The piston rod, one of the most vital components, is typically made of solid or hollow 45# steel. During operation, piston rods are exposed to abrasive wear, significantly impacting their lifespan. To address this, surface coating technologies are employed to enhance wear resistance and prolong service life. This article provides a comparative analysis of hydraulic coating technologies used in China and abroad, focusing on developments in hard chrome plating alternatives, and evaluates them from technical, environmental, and economic perspectives.
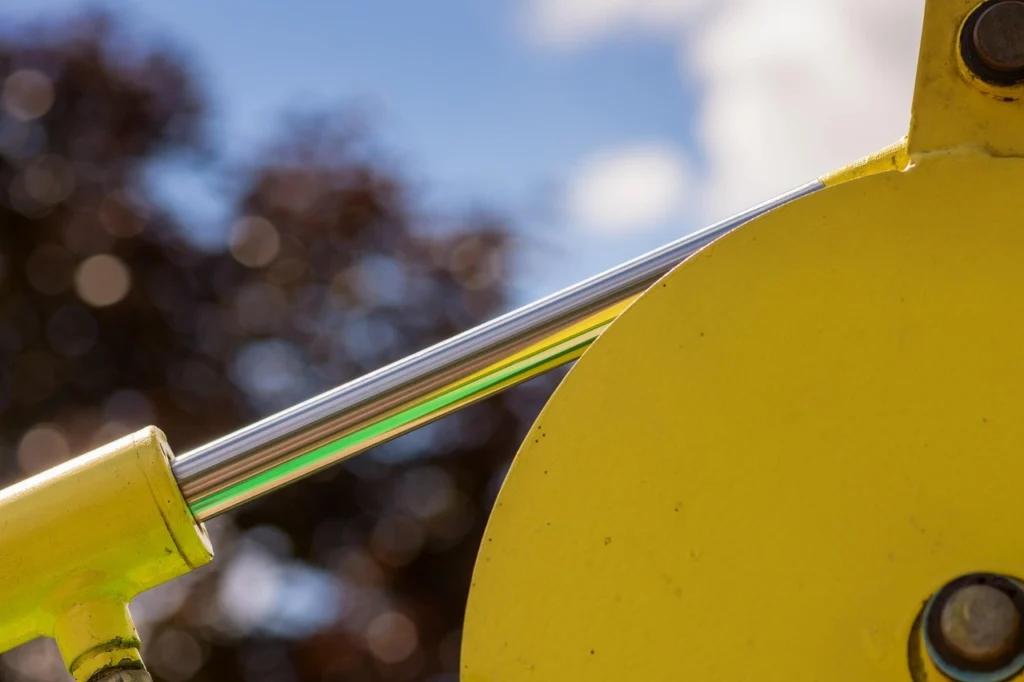
I. Traditional Hard Chrome Plating: Widely Used but Environmentally Hazardous
Hard chrome plating remains the conventional treatment for hydraulic piston rods, offering:
Coating thickness: 0.03–0.05 mm
Surface roughness: Ra 0.1–0.2μm
Advantages: High hardness, excellent wear resistance, bright surface finish
However, its major disadvantages include:
Highly carcinogenic waste: Chromium-based wastewater and emissions pose serious environmental and health risks.
Low efficiency: Cathodic current efficiency is only 18%–20%.
Poor dispersion and coverage: Requires auxiliary electrodes for uniform coating.
Limited corrosion resistance: Due to porous structure and cathodic properties.
Given increasingly strict global regulations on hexavalent chromium, the need for alternative coatings has never been more urgent.
II. Alternatives to Hard Chrome Plating
1. Electroless Nickel-Phosphorus Plating (EN Plating)
Electroless nickel plating is a cutting-edge surface treatment gaining widespread adoption. It provides:
Uniform coating: Ideal for internal bores and complex geometries
High corrosion resistance and hardness: Up to 500Hv (as-plated), 1000Hv (after heat treatment)
Low porosity and strong adhesion
Used in: Automotive cylinders, pistons, crankshafts, spark plugs, molds, oilfield equipment
Limitations:
Slow deposition rate (8–10μm/h)
Higher costs and complex bath maintenance
Brittle coating structure
2. Thermal Spray Coating
This technique uses a high-temperature heat source to spray molten or semi-molten particles onto the substrate. Key advantages:
Versatile materials: Metals, ceramics, and polymers
Minimal substrate heating: Suitable for heat-sensitive components
High wear resistance and customizable properties
Drawbacks:
Porous and layered structure
Requires precise surface preparation
Lower coating uniformity and material efficiency
3. Ceramic Coatings (Plasma-Sprayed Al₂O₃ + TiO₂)
Ceramic coatings for hydraulic piston rods have been successfully applied in high-pressure chemical pumps and marine applications. Features include:
Hardness: 900–1200Hv
Roughness: Ra 0.3–0.35μm
Coating thickness: 200–350μm
Benefits: Superior wear resistance, low friction, and minimal seal wear
Challenges:
Requires excellent surface pretreatment
Coating directionality and porosity issues
4. Tungsten Alloy Electroplating
Initially developed in the U.S. military sector and later expanded in China, tungsten-based coatings offer:
High hardness: >HRC63
Environmental friendliness: No carcinogenic emissions
Cost-effective maintenance: Applied in piston rod refurbishment
Chinese advancements include Ni-W-P, Ni-W-B, and Ni-Fe-W alloy coatings, showcasing strong wear resistance and process improvements.
5. Nickel-Cobalt-Iron (Ni-Co-Fe) Alloy Plating
Emerging in the 2000s, this alloy system has gained traction due to:
High hardness & superior corrosion resistance
Low environmental impact: No class-I controlled pollutants
Efficient production: >95% current efficiency, up to 60μm/h deposition
Excellent surface finish: Even at 3mm thickness
Cost-effective and clean production
This makes Ni-Co-Fe alloy plating a strong candidate to fully replace hard chrome.
Comparison Of Various Coating Treatment Methods Shown In Table
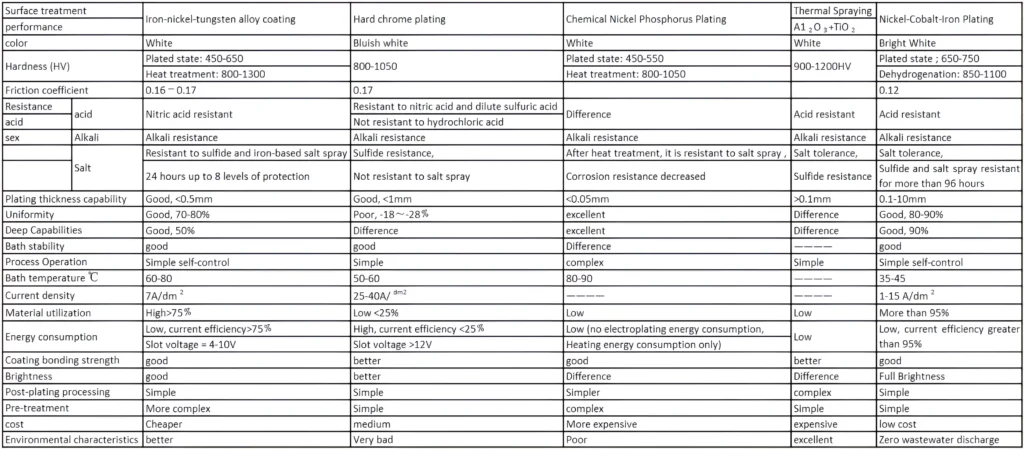
IV. Conclusion
As industries shift towards sustainable and high-performance technologies, clean alternatives to hard chrome are not just desirable—they are inevitable. Among all methods, Nickel-Cobalt-Iron alloy plating stands out for its low cost, high performance, and minimal environmental footprint, making it a promising solution for the future of hydraulic piston rod coatings.
China has made significant advancements in these fields, contributing to the global effort of replacing hazardous coatings with eco-friendly and efficient solutions. As environmental regulations tighten worldwide, manufacturers embracing these next-generation technologies will gain a competitive edge in both domestic and international markets.